What you find on this page:
Air compressors from Atlas Copco are flexible and multipurpose, as various types are suited for different applications. However, as with many intensively used pieces of equipment, air compressors need regular maintenance to preserve their efficiency and effectiveness. This guide will teach you how Atlas Copco troubleshooting works and help you repair it when necessary.
Atlas Copco Air Compressor Troubleshooting: Problems & Solutions
The following are some solutions for troubleshooting Atlas Copco air compressors:
Air Compressor Doesn’t Unload
Compressors can become clogged when they split their power supply with other machinery. For example, an air compressor requires a power supply with 15 or 20 amp breakers.
The unloader valve might also be to blame. First, drain the water and let the air out of the tank to identify any problems. Then, put it back in the closed position and power it up again. The valve needs to be changed if the air compressor still bogs down.
Air Compressor Pressure Output Too Low
In addition to pressure problems, flow difficulties can also be problematic. So even if it appears that the machine is working correctly, it might not be. Air compressors have two possibilities: they build too much air or don’t build any.
Like the pressure, it could only reach a certain PSI (between 90 and 125 PSI).and not much beyond that. Modules such as a pressure valve, intake valve, piston seal, gasket, or tank check valve might be compromised if you notice these problems. Ensure that these modules are not damaged and replace them if necessary.
There are also several possible causes of pressure and flow problems:
- Air formation is delayed when ingestion filters are clogged, putting a strain on the compressor
- A hard-fitting coupler congests the airflow
- The pressure gauge is set too low
Ensure that the pressure setpoint is correct, and consult Atlas Copco’s service department if the valves do not work.
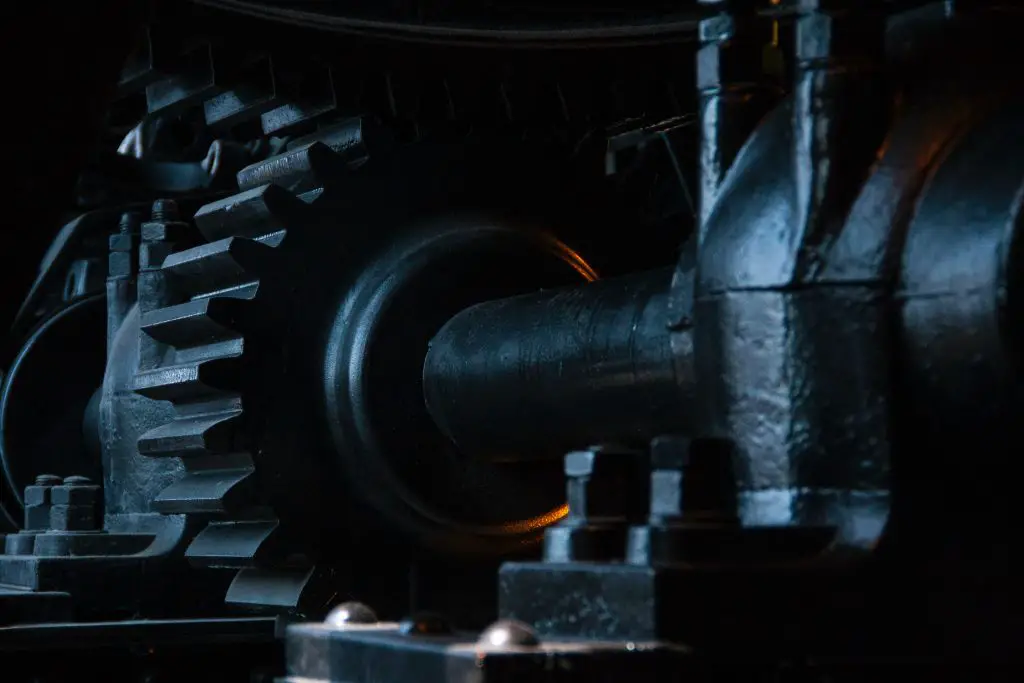
Air Compressor Safety Valve Blows After Loading
The safety valve on the air compressor should be replaced if it trips under operating pressure or the relief set point.
When the tank becomes over-pressurized, the pressure switch does not shut off the motor as the tank fills to its cut-out pressure. Turn the pressure switch off by moving the lever. In case the compressor continues to run, replace the pressure switch.
If the compressor shuts down while you move the pressure switch lever toward the off position, drag the safety valve ring and release all air from the tank. Then, turn on the pressure switch and let the tank fill up.
If the air compressor doesn’t shut off when the tank reaches the cut-out pressure, replace the pressure switch since the switch does not stop the compressor when the tank pressure exceeds.
Air Compressor Stops or Does Not Start
There are usually two causes of this problem: the power cord is detached, or the power switch is disabled. Before starting, make sure the power key and switch are working. Check the breakers as well, if necessary.
Compressors can fail if they lack adequate air pressure. Check the cut-in pressure sets and adjust them accordingly. The lack of oil may also be the cause. And it prevents the compressor from going empty.
The air-intake pump may malfunctioning if the compressor is only active but does not produce any air pressure. Perhaps there is a problem with the gasket between the low-pressure and high-pressure sections of the compressor. Your machine will perform better if you replace them.
Air Flow is Only in Quick Bursts
You must check your meter reading if your air compressor is not providing a steady flow of compressed air. If you find the tank to be much too low, it may not provide you with enough air pressure. In contrast, you should set your air tank’s meter to 90 psi if it reads around 100 psi.
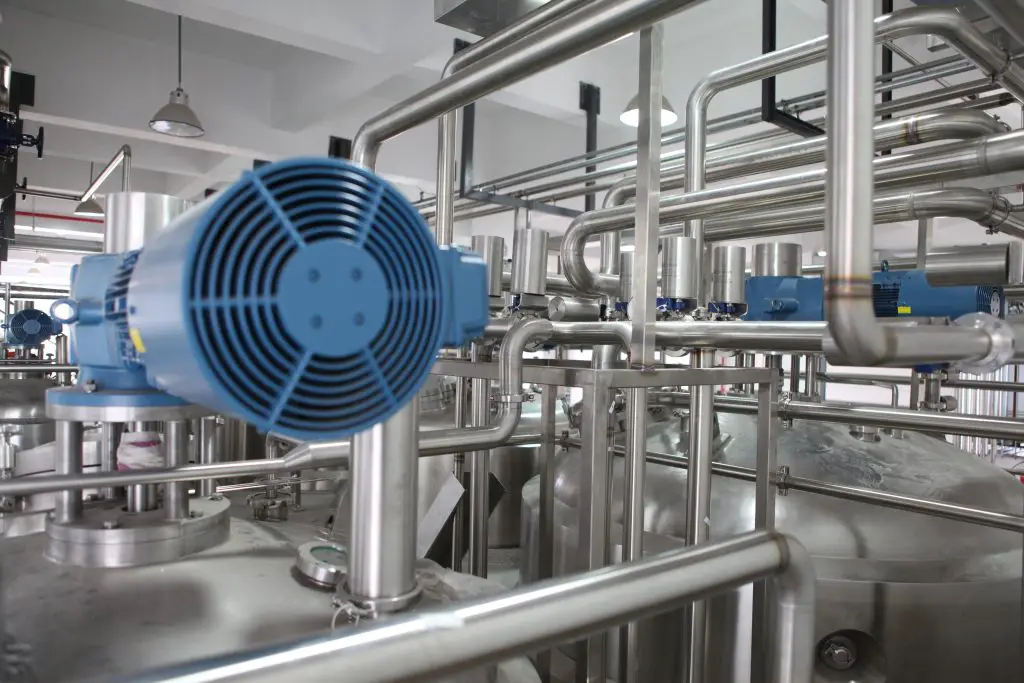
Other problems with Atlas Copco Air Compressor troubleshooting
Air Leaks
1. Compressor Is Constantly Leaking
It is common for the gauge to drop when the compressor shuts off on full charge. However, if the air compressor is disabled, an air is likely. Sometimes, the compressor may even restart automatically to counteract the state. It is necessary to identify the leak’s source.
The air compressor should be unplugged, and all the pressure keys and the couplers should be covered in liquid soap. A leak can be traced wherever bubbles form. If the coupler is bubbling, tighten it up.
A failed check valve in a tank can sometimes trigger an air leak. Check the valve if the pressure gauge keeps dropping even with the tank off. It may be necessary to clean or replace the valve.
Hoses may leak only when connected to compressors, such as when the pressure gauge drops; if this occurs, remove the hose from the compressor.
2. Air Leaks from the Oil Fill Tube
The piston seals must be checked if the compressor loses pressure over the oil fill pipe. The piston seals would most likely be badly damaged and must be replaced as soon as possible. Damaged pistons can cause abrasion, which eventually leads to internal engine deterioration.
3. Air Leaks from the Hood
There are times when small air compressors leak air through the hood. Various methods can be used to identify the problem, including removing the hood, running the air compressor for several minutes, then closing and unplugging it. It is also important to check if air drafts come from the motor parts. You will most likely need to clean or replace the tank valve if the tank valve causes the leak.
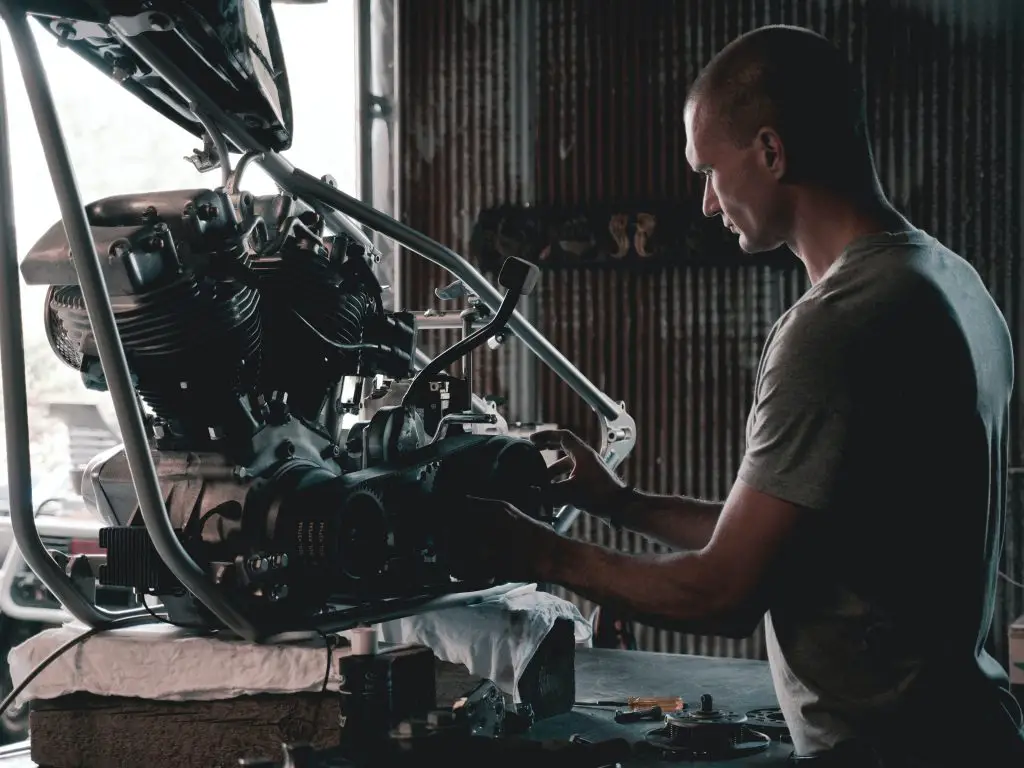
Electrical Motor and Power Problems
1. Compressor Blows Fuses and Breakers
Whenever you encounter blown fuses and breakers, it might be time to replace an electric motor. A worn motor may have loose wires, windings causing it to overheat, and short circuits.
It is important to ensure that the reset mechanism is properly adjusted and functioning correctly and that the motor is not overloaded and adequately vented. Use the correct fuses; they will blow if the amp rating is incorrect.
2. Dimmed Compressor Lights at Startup
Look at the start capacitor to ensure it is not burnt out and is still functioning. The start capacitor deals with the power surge when you turn on the equipment. Sometimes this capacitor will dim the lights when you turn it on due to an initial failure.
3. Breaker Trips at Startup
The air compressor is likely to shut off immediately after starting. To check the issue, shut down the tank, unplug it from the energy source, and remove all air from it. This method will relieve excessive air pressure from the pistons, and the tank can start without further problems. A defective unloader valve is the most common cause of stuck air.
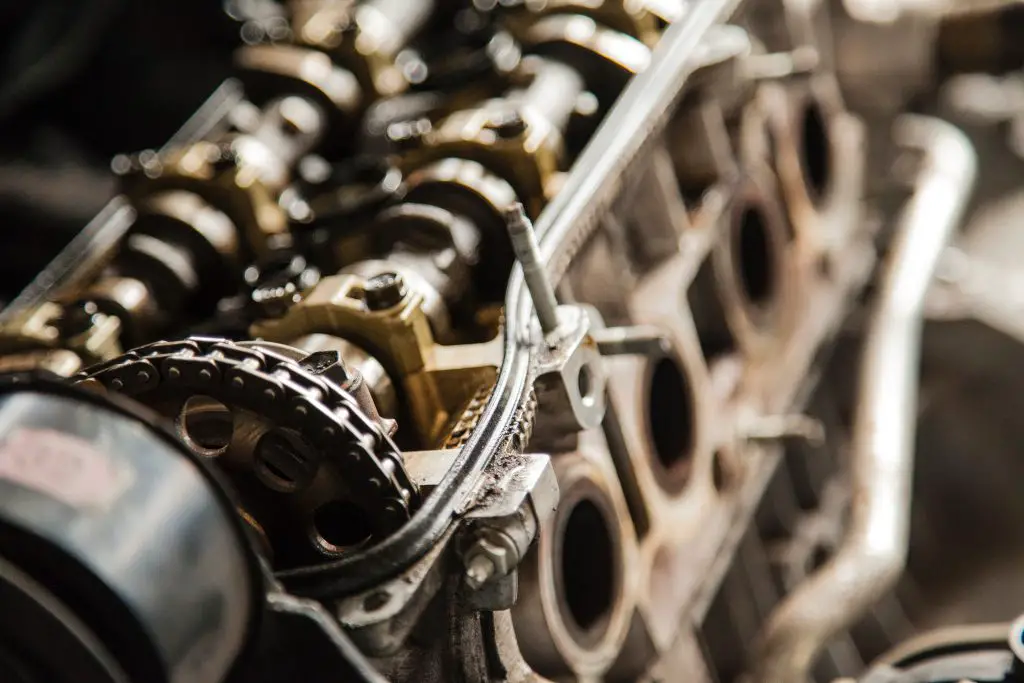
Atlas Copco Won’t Stop
1. Compressor Fails to Stop
After the tank pressure reaches a certain level, the compressor must be switched off. If this doesn’t happen, there are usually a few problems:
i. The pressure release valve is defective
In the absence of pressure release, the motor would keep running. Therefore, until the valve can be replaced, the power must be turned off, and the compressor should not be used further.
ii. Defective pressure switch
Pressure switches need to be replaced if they fail to signal internal controls. In addition, compressors depend on compressed air modules for their operation, and their functions are affected when they malfunction.
Oil in Air Lines
It is possible that you are using the wrong viscosity of oil if there is oil in your air lines. You may need to drain extra oil from the compressor if it has been overfilled, or the oil may escape from the pump. It is important to clean the air filter and check the other modules, especially the seals if the air intake is blocked. It is possible that worn piston rings will have to be replaced, or they may need to be reinstalled if they were placed incorrectly.
Parts and Repair Needed
When an air compressor stops working due to a damaged part, you must verify the source of the problem by checking the part. For example, if any of the following parts were broken, a compressor would not function. In all cases, substitutes are available.
1. Broken Intake Filter
An intake filter removes contaminated particulates from the air entering the compressor. Unfortunately, air compressor intake filters are more easily damaged. Your machine should work with a filter with a similar thread size, portal size, and diameter.
2. Broken Air Compressor Manifold
The manifold kit includes the manifold, two pressure gauges, a regulator, two quick disconnects, and the nipple that connects the whole assembly to the air tank.
3. Broken Compressor Fan
Fortunately, most compressors can be repaired with a replacement fan. Thus, if you have a fan with broken plastic blades, you can replace them with metal blades.
Before buying a new fan, check the Atlas Copco manuals for a list of the part number and equivalent dimensions. Alternatively, measure the original fan’s size and diameter. The number of blades and airflow direction are important to the compressor’s performance.
4. Broken On/Off Switch
Your air compressor will not start if the ON/OFF switch is damaged. So you need to replace it.
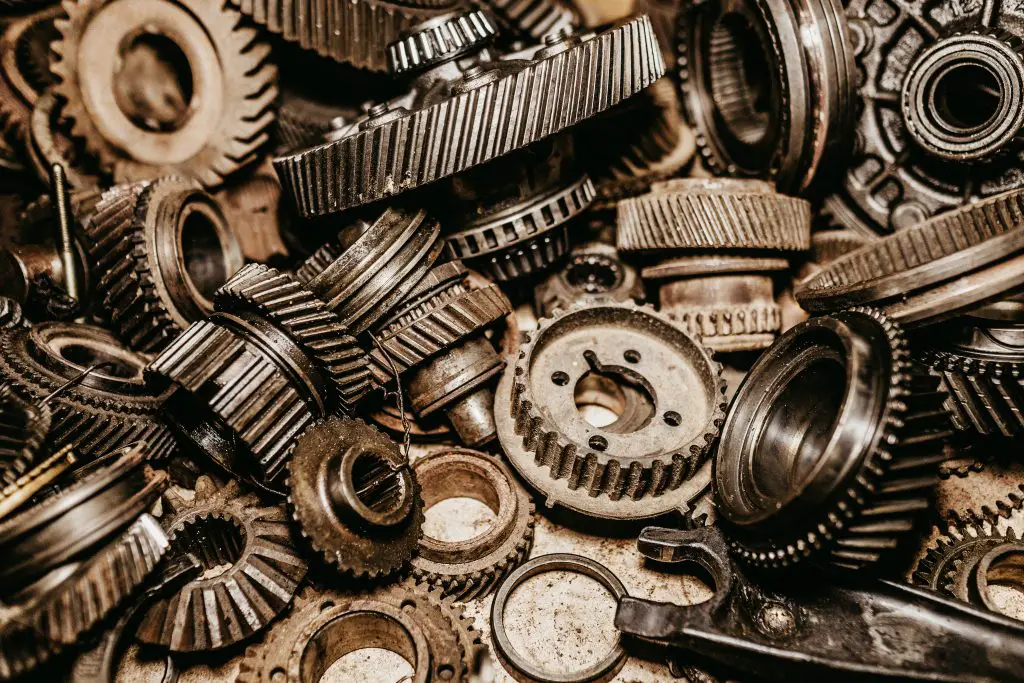
Atlas Copco compressor fault symbols
Atlas Copco compressors display fault codes in their controller’s user function menu during system faults. You can view each fault code individually by pressing up or down if there is more than one active fault code.
Atlas Copco air compressor fault codes are divided into unit faults (ERR/ERROR) and system alarms (SYS/WARNING).
Error Fault
If the air compressor displays an error or shutdown, the error settings will automatically be reset when the problem is resolved, and the air compressor restarts.
System Fault
While the compressor shows a system alarm, the situation is automatically reset once the malfunction has been resolved.
Some fault codes are usually related to problems or faults in the controller itself, which generally prevents the compressor from working, and others are related to issues that occur externally. For example, the Atlas Copco compressor fault codes will likely display two different lights:
LED will flash sluggishly – This indicates an alarm warning state where the compressor continues to operate, but the user still needs to pay attention.
LED flashes fast – This indicates a trip state where the compressor will not run until the fault conditions are resolved.
The fault codes are usually tagged with unique numeric codes, which can be understood from the user’s manual for the specific Atlas Copco compressor.
Conclusion
If you’re having trouble with your Atlas Copco air compressor, don’t panic! This troubleshooting guide has walked you through some common issues and solutions.
Hopefully, by following these steps, you can get your machine up and running again as soon as possible. If not, be sure to consult a professional for additional assistance. Thanks for reading!
Frequently Asked Questions
Transportable air compressors must operate at full capacity to drive nails over wood or increase tire pressure. To troubleshoot an air compressor first, check the power button and switch, as well as the breakers, if necessary.
An almost empty oil tank might cause the air compressor not to work. A lack of contact between the pressure switch and the inner circuit may be causing the compressor to fail to power on. Perhaps amending the pressure switch can resolve this issue.
A condensation buildup inside the compressor’s pressure lines will likely cause water spraying. Even though the water does not specify a compressor fault, it would be best to drain the compressor to get any extra water out of the lines. You can do it yourself by using a water trap and regulator or draining the tank.
When your compressor’s air intake filter is clogged with dirt and dust, it strains the motor, causing it to draw more power than usual. If this extra power draw exceeds the breaker’s capacity, it trips the breakers.
You must turn off the power supply to the air compressor, re-fit the guard, and switch on the compressor’s power supply. Then turn on the water cooling and air blast cooling. Once the compressor is started, close the air discharge valve and slowly open it until the air pressure between the compressor and the air net is equal; now, the compressor will work.
1. Press the RESET button.
2. By pressing the button, the stored alarm indication is canceled.
3. Pressing the button for more than 3 seconds tests the central control unit: all LEDs must be on.